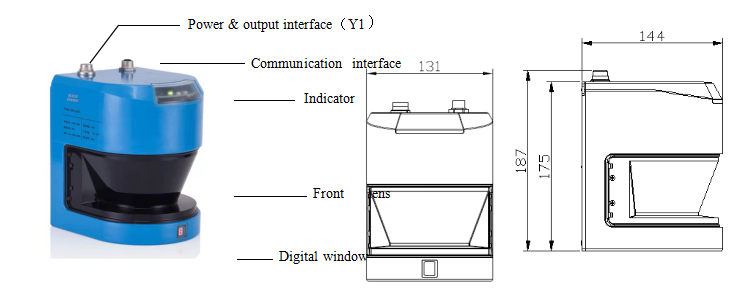
Pin | Terminal No | Color | definition | Function |
![]() | 1 | Blue | 24V- | Negative input of power supply |
2 | Black | HEAT- | Negative input of heating power | |
3 | White | IN2/OUT1 | I/O input / NPN output port 1(same to OUT1) | |
4 | Brown | 24V+ | Positive input of power supply | |
5 | Red | HEAT+ | Positive input of heating power | |
6 | Green | NC/OUT3 | I/O input / NPN output port 3(same to OUT1) | |
7 | Yellow | INI/OUT2 | I/O input / NPN output port2(same to OUT1) | |
8 | NC | NC | - |
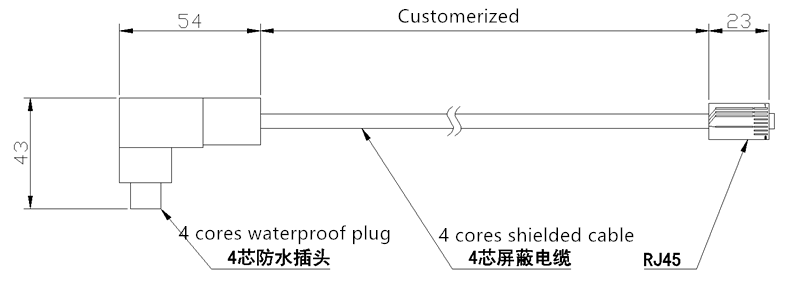
4.1 Function
The main functions of LSD1XX A series products are distance measurement, input setting, and comprehensive judgment of vehicle entry and exit process and dynamic separation of vehicles by measuring vehicle width and height information. LSD1XX A series radar is connected to the upper computer through Ethernet cable, and the data graphs and measurement data can be displayed through the upper computer software.4.2 Measurement
4.2.1 Distance measurement(Apply to LSD101A、LSD121A、LSD105A、LSD151A)
After the radar is powered on and passes the system self-test, it starts to measure the distance value of each point within the range of - 5 ° ~ 185 °, and output these values through the Ethernet interface. The default measurement data is 0-528 groups, corresponding to the distance value in the range of - 5 ° ~ 185 °, which is in hexadecimal format, and the unit is mm. For example: Fault report Receive data frame :02 05 00 FE 00 FE 19 FE DB FE 01 02 F9 02 DE 02 E5 02 DE 02 E5 02 E5 02 E5 02 EC 02 EC 02 F3…….. Corresponding distance value: Date:02 F9 02 DE 02 E5 02 DE 02 E5 02 E5 02 E5 02 EC 02 EC 02 F3。。。 Angle and distance information corresponding to data:-5° 761mm,-4.64° 734mm, -4.28° 741mm , -3.92°734mm , -3.56°741,-3.20° 741mm, -2.84° 741mm,-2.48° 748mm,-2.12° 748mm,1.76° 755mm。。。4.2.2 Width and height measurement(Apply to LSD131A)
4.2.2.1 Measurement communication protocol Description | Function code | Width result | Height result | Parity bit |
Bytes | 2 | 2 | 2 | 1 |
Radar sending(Hexadecimal) | 25、2A | WH、WL | HH、HL | CC |
Description | Function code | Auxiliary function code | Parameter | Parity bit |
Bytes | 2 | 1 | 6/ 0 | 1 |
Radar receiving(Hexadecimal) | 45、4A | A1(setting) | DH、DL、KH、KL、GH、GL | CC |
Radar receiving(Hexadecimal) | 45、4A | AA(query) | —— | CC |
Radar sending(Hexadecimal) | 45、4A | A1 / A0 | DH、DL、KH、KL、GH、GL | CC |
Relationship curve between detection object and distance
Relationship curve between detection object reflectance and distance
Relationship curve between light spot size and distance
3.1 Output interface definition
3.1.1 Function description
No | Interface | type | Function |
1 | Y1 | 8 pin sockets | Logical interface:1. Power supply2. I/O input(apply toLSD121A)3. Heating power |
2 | Y3 | 4 pin sockets | Ethernet interface:1.Measurement data sending2. Reading of sensor port setting, area setting and. fault information |
3.1.2 Interface definition
3.1.2.1 Y1 interface 7-cores interface cable: Note :For LSD101A、LSD131A、LSD105A, this port is NPN output port(open collector),there will be low lever output when object is detected at the detection area. For LSD121A, LSD151A , this port is I/O input port, When the input is suspended or connected to low, it is identified as high level and output as "1" in the communication protocol; When the input is connected to 24V +, it is identified as low level and outputs as "0" in the communication protocol. 4-cores interface cable: Pin | No | Color | Signal definition | Function |
![]() | 1 | Orange white | TX+E | Ethernet data sending |
2 | Green white | RX+E | Ethernet data receiving | |
3 | Orange | TX-E | Ethernet data sending | |
4 | Green | RX-E | Ethernet data receiving |
3.2 Wiring
3.2.1 LSD101A、LSD131A、LSD105A Switching output wiring(7 cores power cable)
Note: ●When the switch output line is not used, it shall be suspended or grounded, and it shall not be short circuited with the power supply directly; ●V + is not more than 24VDC voltage, and must be grounded together with 24VDC. 3.2.2 LSD121A ,LSD151A Switching output wiring(7 cores power cable) 3.2.3 LSD121A、LSD151A external electronic wiring diagram(7-cores power cable) The lidar input cable should be connected with external Vout cable meanwhile connect one 5K resistance to 24+No | Components | Instruction |
1 | Logic interface(Y1) | Power and I/O input cables are connected with radar by this interface |
2 | Ethernet interface(Y3) | Ethernet communication cable are connected with radar by this interface |
3 | Indicator window | System operation, Fault alarm and system output three indicators |
4 | Front lens cover | Emitting and receiving light beams realize the scanning of objects by this lens cover |
5 | Digital indication window | The status of Nixie tube is shown at this window |
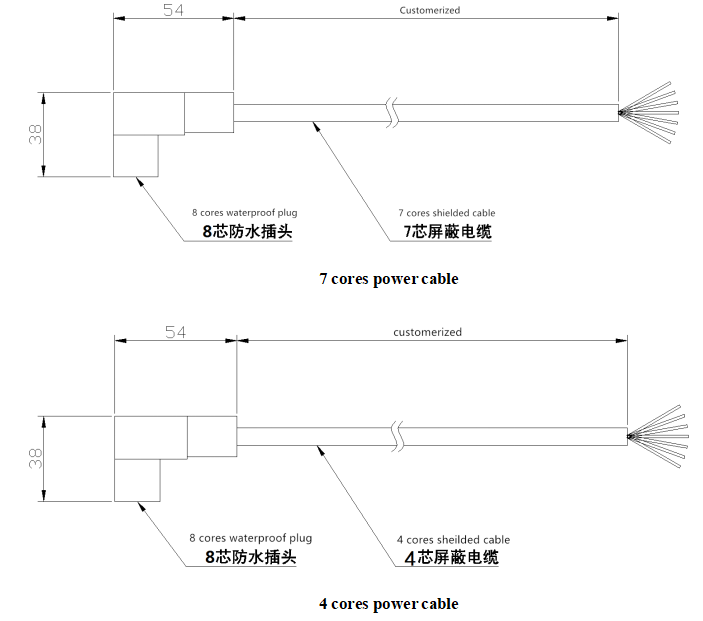
Pin | Terminal No | Color | definition | Function |
| 1 | Blue | 24V- | Negative input of power supply |
2 | White | HEAT - | Negative input of heating power | |
3 | NC | NC | Blank | |
4 | Brown | 24V+ | Positive input of power supply | |
5 | Yellow | HEAT+ | Positive input of heating power | |
6 | NC | NC | Blank | |
7 | NC | NC | Blank | |
8 | NC | NC | Blank |
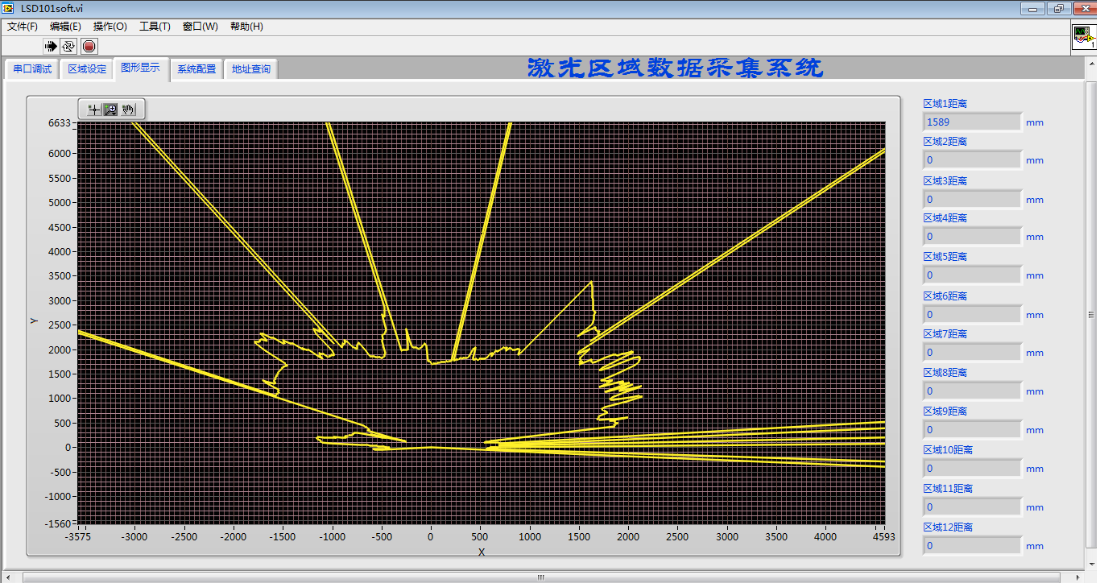
Model | LSD101A | LSD121A | LSD131A | LSD105A | LSD151A | |
Supply voltage | 24VDC±20% | |||||
Power | < 60W, Normal working current <1.5A,Heating <2.5A | |||||
Data interface口 | Ethernet,10/100MBd,TCP/IP | |||||
Response time | 20ms | |||||
Laser wave | 905nm | |||||
Laser grade | Grade 1(safe to people eyes) | |||||
Anti-light interference | 50000lux | |||||
Angle range | -5° ~ 185° | |||||
Angle resolution | 0.36° | |||||
Distance | 0~40m | 0~40m | 0~40m | 0~50m | 0~50m | |
Measurement resolution | 5mm | |||||
Repeatability | ±10mm | |||||
In put function | – | I/O 24V | – | – | I/O 24V | |
Output function | NPN 24V | – | NPN 24V | NPN 24V | – | |
Area division function | ● | – | – | ● | – | |
Width&height measurement | Vehicle detection speed | – | – | ≤20km/h | – | |
Vehicle width detection range | – | – | 1~4m | – | ||
Vehicle width detection error | – | – | ±0.8%/±20mm | – | ||
Vehicle height detection range | – | – | 1~6m | – | ||
Vehicle height detection error | – | – | ±0.8%/±20mm | – | ||
Dimension | 131mm × 144mm × 187mm | |||||
Protection rating | IP68 | |||||
Work/storage temperature | -30℃ ~ +60℃ /-40℃ ~ +85℃ |
Trouble codes
No | Trouble | Description |
001 | Parameter configuration fault | Configuration of machine working parameters through upper computer is incorrect |
002 | Front lens cover fault | The cover is polluted or damaged |
003 | Measurement reference fault | The measurement data of bright and dark reflectors inside the machine is incorrect |
004 | Motor fault | The motor does not reach the set speed, or the speed is unstable |
005 | Communication fault | Ethernet communication, measurement data transmission blocked or disconnected |
006 | Output fault | Output short circuit or off |
9.2 Troubleshooting
9.2.1 Parameter configuration fault
Reconfigure the working parameters of the radar through the upper computer and transmit them to the machine。9.2.2 Front lens cover fault
The front mirror cover is an important part of LSD1xxA. If the front mirror cover is polluted, the measurement light will be affected, and the measurement error will be large if it is serious. Therefore, the front mirror cover must be kept clean. When the front mirror cover is found dirty, please use a soft cloth dipped with neutral detergent to wipe in the same direction. When there are particles on the front mirror cover, blow them off with gas first, and then wipe them to avoid scratching the mirror cover.9.2.3 Measurement reference fault
The measurement reference is to verify whether the measurement data is valid. If there is a fault, it means that the measurement data of the machine is not accurate and cannot be used any more. It needs to be returned to the factory for maintenance.9.2.4 Motor fault
Failure of the motor will cause the machine to fail to scan for measurement or result in inaccurate response time. Need to return to factory for maintenance。9.2.5 Communication fault
Check the communication cable or machine failure
9.2.6 Output fault
Check the wiring or machine failure No | Name | Model | Note | Weight(kg) |
1 | Radar Sensor | LSD101A | Common type | 2.5 |
2 | LSD121A | In-put type | 2.5 | |
3 | LSD131A | Width & height measurement type | 2.5 | |
4 | LSD105A | Long distance type | 2.5 | |
5 | LSD151A | In-put type Long distance type | 2.5 | |
6 | Power cable | KSP01/02-02 | 2m | 0.2 |
7 | KSP01/02-05 | 5m | 0.5 | |
8 | KSP01/02-10 | 10m | 1.0 | |
9 | KSP01/02-15 | 15m | 1.5 | |
10 | KSP01/02-20 | 20m | 2.0 | |
11 | KSP01/02-30 | 30m | 3.0 | |
12 | KSP01/02-40 | 40m | 4.0 | |
13 | Communication cable | KSI01-02 | 2m | 0.2 |
14 | KSI01-05 | 5m | 0.3 | |
15 | KSI01-10 | 10m | 0.5 | |
16 | KSI01-15 | 15m | 0.7 | |
17 | KSI01-20 | 20m | 0.9 | |
18 | KSI01-30 | 30m | 1.1 | |
19 | KSI01-40 | 40m | 1.3 | |
20 | Protective cover | HLS01 | 6.0 |