
Sensor Length | Visible Brass Length | Overall Length(including ends) |
6'(1.82m) | 70''(1.78m) | 76''(1.93m) |
8'(2.42m) | 94''(2.38m) | 100''(2.54m) |
9'(2.73m) | 106''(2.69m) | 112''(2.85m) |
10'(3.03m) | 118''(3.00m) | 124''(3.15m) |
11'(3.33m) | 130''(3.30m) | 136''(3.45m) |
Model No. | QSY8311 |
Section size | ~3×7mm2 |
Length | can be customized |
Piezoelectric coefficient | ≥20pC/N Nominal value |
Insulation resistance | >500MΩ |
Equivalent capacitance | ~6.5nF |
Working temperature | -25℃~60℃ |
Interface | Q9 |
Mounting bracket | Attach the mounting bracket with the sensor (Nylon material not recycled). 1 pcs bracket each 15 cm |
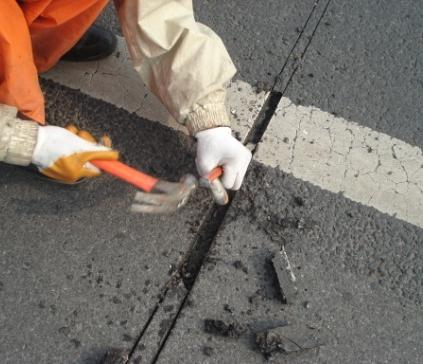
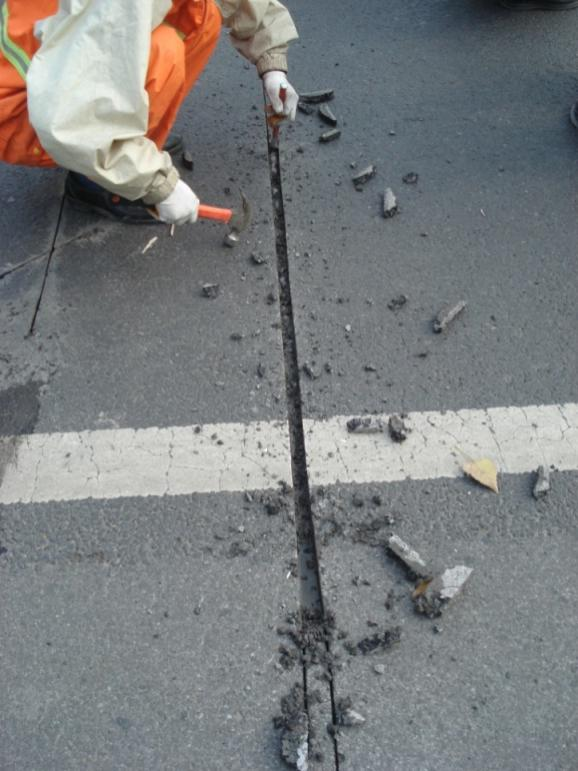
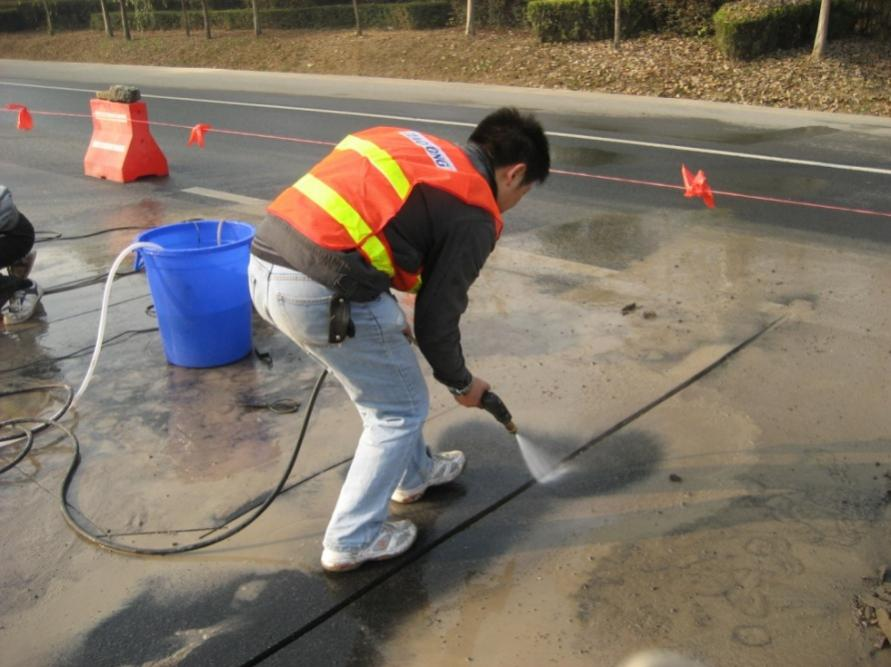

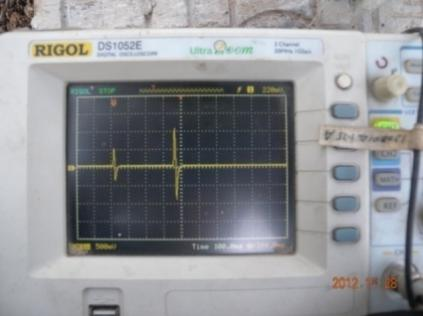
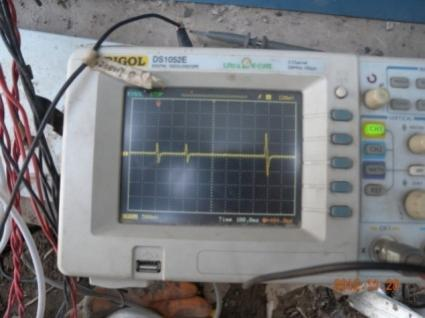
2 Axes
3 Axes
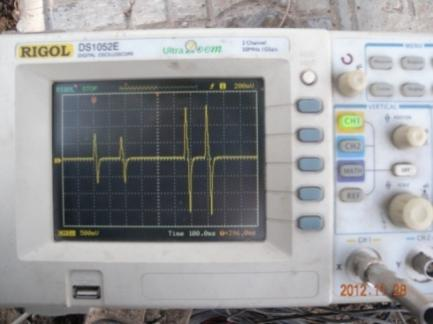
4 Axes
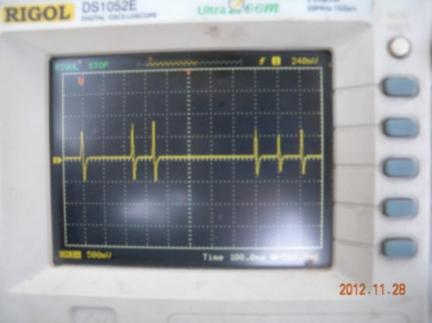
6 Axes